admin | Publié le |
COMMENT MESURER VOTRE TRS
Tout d’abord, il existe une différence notable entre savoir « théoriquement » la manière de mesurer le TRS (Taux de Rendement Synthétique) d’un équipement et le mesurer réellement en pratique. Cet article donnera des conseils et des points cruciaux sur la manière de mesurer votre TRS dans un atelier de production.
Comme souvent dans les ateliers, il est rare que des données fiables soient utilisées. Cela est particulièrement vrai dans le calcul du TRS, car il est difficile d’obtenir les données requises. En conséquence, nous ne faisons généralement confiance à aucune donnée TRS dans un atelier, à moins de connaître les calculs qui le sous-tendent. La plupart des indicateurs calculés d’un TRS sont d’une qualité si faible qu’ils ne valent pas la peine. Il n’est donc pas si facile d’obtenir les données d’un TRS.
Dans le précédent article, nous avions examiné la définition du TRS, y compris les pertes de disponibilité, de cadence et de qualité. Dans ce post, nous présenterons comment mesurer un TRS. Les articles suivants détailleront les trois principales mesures de la tromperie du TRS, ainsi que des avantages à en tirer.
Quelle base de temps pour le calcul du TRS ?
La première question à laquelle vous devez répondre est la base de temps de votre calcul du TRS. Souhaitez-vous caculer votre TRS uniquement sur la base des équipes (1×8, 2×8, …) planifiées ou souhaitez-vous envisager une base de calcul 24/24, 7/7 et 365 jours par an ?
Dans la plupart des cas dans l’industrie, la base de calcul est basée sur les équipe. Si l’opération est programmée pour travailler sur deux équipes cinq jours par semaine, la base de temps est constituée de ces deux équipes de cinq jours. Toutefois, si votre système manque de capacité et ne peut pas répondre à la demande de ses clients, il peut être approprié de commencer avec une base de temps 24h / 24 et 7j / 7. Cependant, préparez-vous à l’opposition de votre hiérarchie. Une base de temps 24 heures sur 24 et 7 jours sur 7 fera baisser votre TRS, donc sur le papier, cela semble pire même si le système n’a pas changé, seul la base de calcul. Étant donné que vos collaborateurs peuvent être jugés sur le TRS, ils ont peut-être eux aussi intérêt à rechercher un bon indicateur de TRS (et peut-être même à vous aussi ! …).
Dans tous les cas, quelle que soit votre base de temps, vous devez déterminer ce que vous auriez pu produire pendant cette période.
Cadence de base pour le TRS
La deuxième donnée importante dont vous avez besoin est la cadence nominale de production de votre équipement. Que pourrait produire ce même équipement de production si tout le reste était parfait ? L’approche consiste à prendre toutes les données que vous pouvez avoir enregistré. Cependant, selon notre expérience, ces chiffres sont généralement incorrects ou obsolètes. Ils peuvent être simplement la moyenne d’une bonne journée de production. Cependant, même une bonne journée de production entraîne des pertes, et prendre la moyenne les ignorerait. Elles peuvent être basées sur un calcul théorique, peut-être en utilisant les méthodes MTM ou REFA, qui sont souvent beaucoup plus lentes qu’un bon opérateur et incluent des estimations et des pauses personnelles.
Pour obtenir une bonne estimation de la vitesse maximale nominale d’un process de production, vous devez mesurer à plusieurs reprises le temps écoulé entre l’achèvement des pièces. Vous constaterez que ce temps est distribuée statistiquement (nous n’entrerons pas dans les détails statistiques ici). La plupart des temps se sont concentrés autour de la moyenne, certains ont pris plus de temps, quelques-uns beaucoup plus, peut-être en raison d’une panne, et certains ont été plus rapides ou beaucoup plus rapides que la moyenne. Le but est d’obtenir le temps le plus court possible. Cependant, si vous prenez simplement la plus petite valeur de votre ensemble de mesures, vous avez probablement une erreur de mesure. Il est préférable de trier les mesures et de prendre le temps où 95% ou 90% de toutes les mesures sont plus lentes que ce temps (statistiquement parlant, on se concentre généralement sur le second quartile).
Le TRS lui-même
Maintenant, vous avez la base de temps et la base de cadence. En divisant la base de temps par la cadence, vous obtenez le nombre théorique de pièces qui auraient pu être produites. Par exemple, si vous avez décidé d’analyser deux équipes postées de 8 heures par jour pendant 5 jours, vous disposez d’un total de 80 heures ou de 4 800 minutes. Si votre process de production a une vitesse maximale d’une pièce toutes les 2,5 minutes, vous divisez 4800 minutes par 2,5 minutes par pièce et vous obtenez 1920 pièces que vous auriez pu produire au cours de cette même période.
Ces 1920 pièces théoriques sont maintenant comparées à la production réelle pendant cette période. Il est généralement facile d’obtenir ce chiffre, car même les plus « mauvaises » usines ont une idée approximative de ce qu’elles ont produit.
Dans l’exemple ci-dessus, supposons que vous ayez produit non pas 1920 mais seulement 1132 pièces, votre TRS serait alors 1132/1920 soit 59%.
Bien sûr, vous pourriez aussi être intéressé par les pertes qui vous ont empêché de produire 788 pièces au cours de cette semaine. Il est maintenant un peu plus difficile d’obtenir des données fiables.
Enregistrement informatique des données
Si vous êtes chanceux, vous pouvez avoir un système d’enregistrement des données de votre équipement de production qui établit un protocole automatique de ce que la machine fait et quand. Cependant, selon notre expérience, même s’il existe un système d’enregistrement de données numériques, celui-ci ne dispose généralement pas de suffisamment de données pour calculer les pertes de manière fiable. Par exemple, les problèmes de qualité ne généralement peuvent pas être détectés que par la suite et ne seront pas consignés dans le système informatique. Le process de production peut ne pas savoir si un arrêt était dû à un opérateur manquant ou à une machine manquante. Selon toute vraisemblance, avec un système de données numériques, vous avez encore des lacunes et vous devez trouver au moins certains détails de manière différente que l’enregistrement informatique de données.
Observations manuelles
L’observation manuelle sur une période plus longue est probablement la méthode de référence en matière de mesure du TRS. Dans cette observation, un opérateur se tient à côté de l’équipement de production pour établir un protocole indiquant quand la machine fait quoi. Il ou elle doit noter toute irrégularité (par exemple, lorsque la machine s’arrête, que l’opérateur est absent, qu’il manque du matériel ou que des produits sont mis au rebut). Ce seront probablement les données les plus fiables que vous puissiez obtenir. Cependant, cet étalon-or est livré avec un prix plaqué or, car vous devez payer pour qu’un opérateur 24 heures sur 24 se place à côté de la machine pour prendre les notes.
Si vous souhaitez néanmoins effectuer cette observation manuellement, voici quelques conseils pratiques :
- Tout d’abord, préparez très attentivement vos observations pour le recueil des données, éventuellement avec des tests ou observations préalables plus court(e)s. Cela ne sert à rien d’avoir trois jours de données alors qu’il manque des informations cruciales ;
- État d’esprit Kaizen à respecter : Inclure les opérateurs systématiquement (voir les représentants du personnel dans certains cas). Observer une machine seule ne devrait pas poser de problème, mais peu d’équipement de production opèrent sans surveillance. En fait, vous établissez un protocole 24 heures sur 24 indiquant ce que l’opérateur fait et ne fait pas. Faites participer les opérateurs et représentants du personnel afin qu’ils comprennent ce que vous faites et pourquoi. Ne le faites jamais contre la volonté des opérateurs, car ils ont la capacité de gâcher votre mesure au-delà de la convivialité. Il est utile que la personne qui observe soit également un opérateur et un collègue, et non un outsider ou un superviseur ;
- Assurez-vous pourquoi vous mesurez le TRS, quel est le problème réel à traiter ? Cet effort pour obtenir les détails des pertes de TRS n’est utile que dans un premier temps si vous planifiez un projet pour améliorer lesdites pertes dans un deuxième temps. Si la seule raison de mesurer le TRS est parce que quelqu’un de plus haut veut un numéro, alors il existe des moyens beaucoup moins chers pour en obtenir un.
Enregistrement des données par les opérateurs eux-mêmes
Les enregistrements par des opérateurs s’agit probablement du moyen le plus courant dans l’industrie de déterminer les détails des pertes d’un TRS. L’opérateur de la machine établit un « protocole des perturbations rencontrées », qui sont ensuite convertis en enregistrements numériques et analysés. Pour des raisons pratiques, les opérateurs n’enregistrent que les perturbations dépassant une certaine longueur (c’est-à-dire s’il y a un arrêt supérieur à 5 ou 15 minutes ; l ‘échelle des mesures devant être validées au préalable par les services Méthodes et Amélioration Continue / Lean). L’avantage est que ces données peuvent être obtenues avec peu d’effort, seule l’analyse des données nécessite un certain temps. En revanche, tous les arrêts en dessous du temps limite (ralentissements et micro-arrêts) sont ignorés et la qualité de l’observation peut varier d’un opérateur à l’autre.
Mettez toutes ces données en musique
Lors du calcul du TRS, il est probablement plus facile d’obtenir la capacité disponible et les pièces produites. Les pertes de qualité sont également souvent disponibles à travers l’observation des rebuts ou des bacs rouges, ou peuvent être obtenues par les enregistrements des opérateurs. Les pertes de disponibilité sont un peu plus difficiles, mais l’observation manuelle ou les enregistrements des opérateurs peuvent aussi généralement donner une bonne illustration.
La partie la plus délicate est la perte de cadence (ralentissement, micro-arrêts). Les enregistrements des opérateurs et les observations manuelles ont du mal être saisis directement par une observation. Ce que nous savons avec certitude, c’est qu’ils doivent constituer le reste de l’écart entre la capacité disponible et les pièces produites. Dans l’exemple ci-dessous, même si nous ne connaissions pas les pertes de vitesse, nous pourrions facilement en conclure qu’elles sont de 10%, car ces 10% ne sont que le reste de l’écart. Bien que cela nous indique la valorisation des pertes de cadence, cela ne nous aide pas à détailler les causes des pertes de cadence. Malheureusement, ces pertes de cadence de production sont rarement marginales et peuvent facilement représenter jusqu’à 30% ou 50% des pertes totales. Dans ce cas, vous devez approfondir vos investigations sur les pertes de cadence de votre équipement de production.
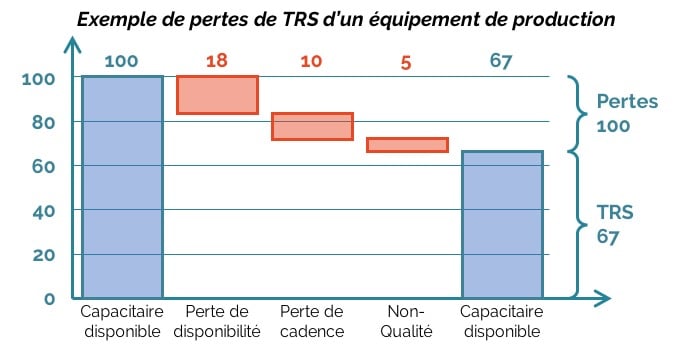
Laisser un commentaire